Refining the design, finalising prototyping and building final robot
Drivebase & robot assembly
Proper alignment of swerve modules is a tedious task that has to be repeated several times throughout the build season. It is the process of correctly positioning the steer and drive components of a swerve module to ensure that the robot moves in the intended direction. In order to simplify it, special tools were designed and 3D-printed. Misaligned swerve modules can cause the robot to veer off course or not move at all. The team’s unwavering commitment and drive have resulted in a truly impressive feat.
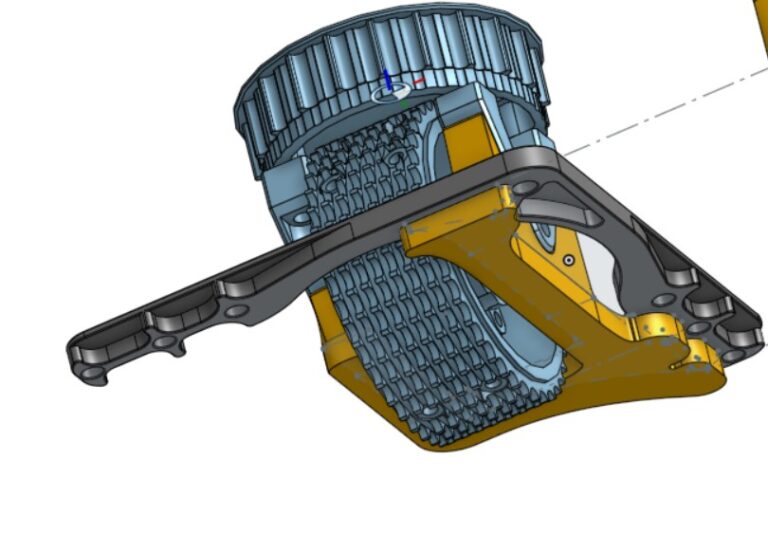

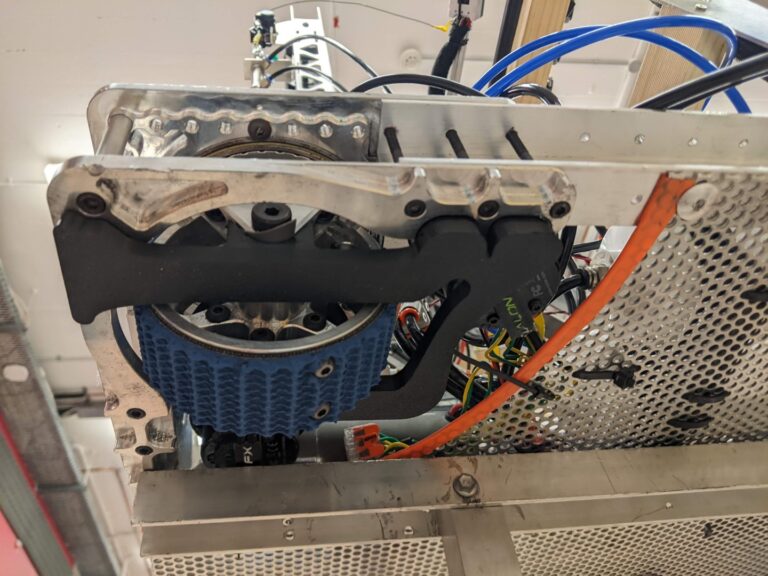
Embracement
This week in the emplacement team, we designed and manufactured a new mast that was installed onto the drive base of the new robot. Also, towards the end of the week, we have finalised the design of the arm and how to extend that arm and are in the process of fabricating it with our CNC router. In the end effector section, you can find updates about intake and extend.
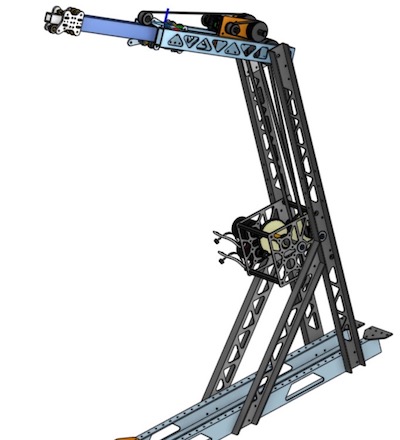
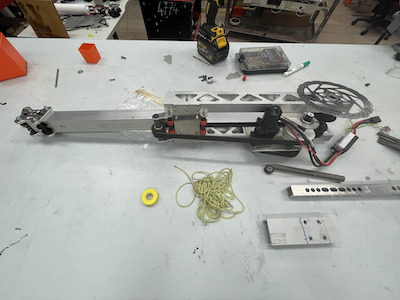
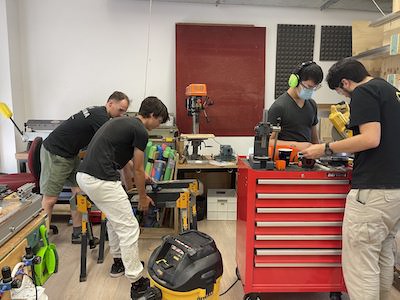
End effector
In this week ,the end effector team spent a majority of their time creating and improving our designs for an activation switch that could activate the claw. We first thought about a switch that activated inside the claw but after testing, it proved unreliable. We then decided and built a switch that would activate on the shelf rather than the cone.
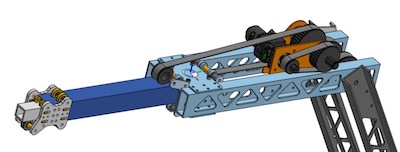
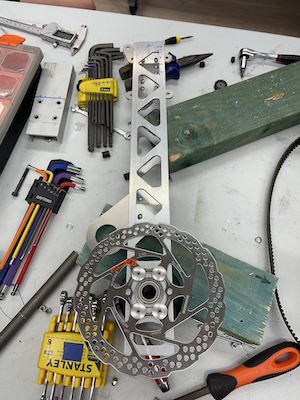
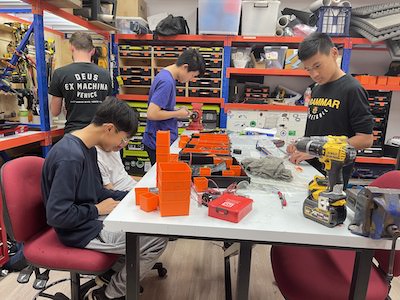
Software
The team has written the state machines for high-level control, auto alignment of the robot and autonomous mode and they’re in the process of testing them. They have also continue to work on improving the April tag( visit here if you are wondering what april tag is) vision system and have made significant progress in tracking scored game pieces.
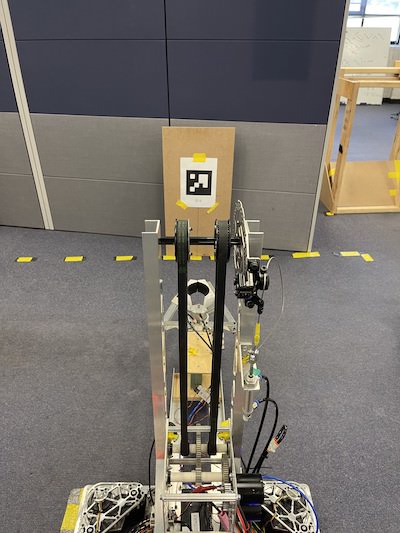
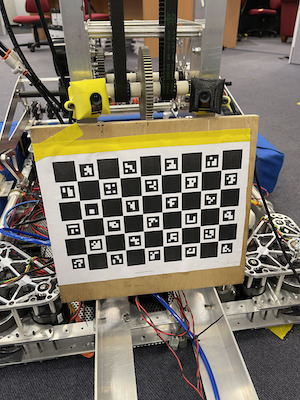
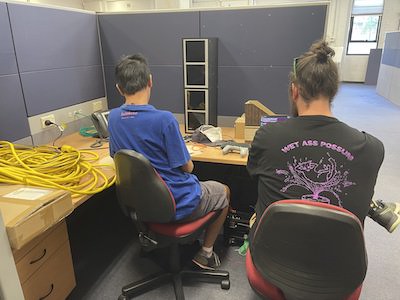
A huge round of applause to the team for their outstanding success. Your work is an inspiration to us all and a shining example of what can be achieved through teamwork and determination. Congratulations!